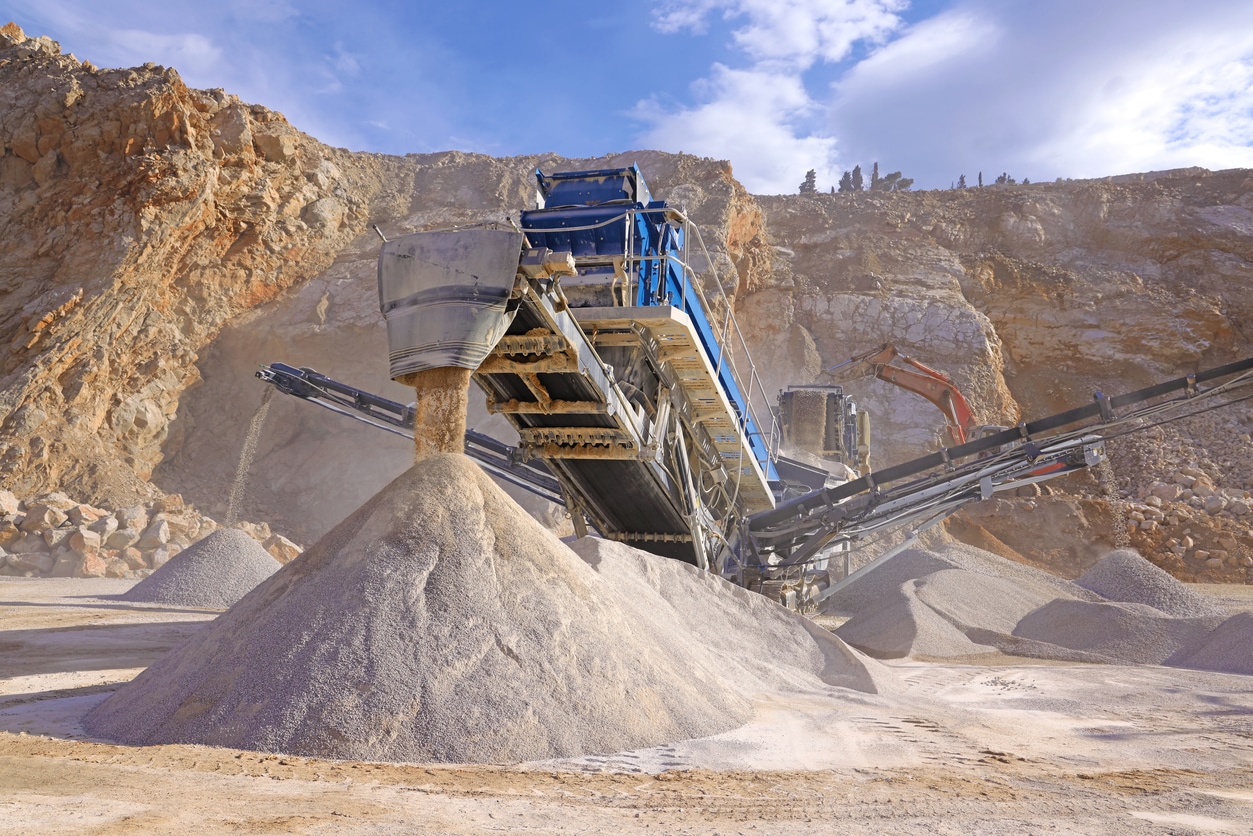
If you are in the aggregate or demolition industry, you need a rock crusher that can reduce large pieces of stone and concrete down to more manageable, useful, and profitable sizes. Understanding the different types of rock crushers can help you figure out which is the right crusher for you.
Most of the time, people divide rock crushers into these three types:
- Jaw rock crushers
- Impact rock crushers
- Cone rock crushers
Understanding how these work can help you decide which type is best for your application.
Jaw Rock Crushers
A jaw rock crusher has a fixed plate and a movable jaw. When you introduce materials into the crusher, the jaw presses them against the fixed plate until they break. The fragments then fall deeper into the gap between the jaw and plate. The jaw motion repeats until the introduced material is small enough to fall through the gap at the bottom, which you can set to determine how much reduction you get from your crusher.
Jaw rock crushers are popular as primary rock crushers. This means that they get the raw material from the quarry, mine, or demolition site, as opposed to secondary rock crushers, which get their material from a previous crusher. People choose jaw rock crushers as primary crushers because they can take highly variable inputs. However, they aren’t good at producing smooth, small, or uniform aggregate, which is why it’s popular to use a secondary rock crusher alongside the jaw rock crusher. Even with the need for a secondary rock crusher, the relatively low maintenance cost and ability to handle highly variable input make jaw rock crushers a popular choice.
Impact Rock Crushers
Impact rock crushers break rock by hitting it with one or more rotary hammers. After being struck by a hammer, the broken rock pieces bounce around the interior of the crusher, typically getting struck again and again. The rock keeps bouncing around until it gets small enough that it travels through the sorter openings to exit the machine.
Impact rock crushers work well as primary crushers, but they can also be used as secondary or finishing rock crushers, too. They can take a wide range of material sizes and types and can produce a lot of rock. With impact rock crushers, you can have good control over the size of the product, and it’s relatively uniform. That’s what makes them popular as secondary and finishing rock crushers.
The big disadvantage of impact rock crushers is that they are relatively expensive to operate. The hammers (often called blow bars) wear out quickly and often need to be replaced. This isn’t a simple operation, and if you don’t have access to people with the skill to change them out, it can slow your operation down as you wait for a mobile mechanic to come out to handle it, or you tow it to a shop for changing them.
Cone Rock Crushers
A cone rock crusher is a compression crusher like the jaw crusher, but it works in a very different manner. In a cone rock crusher, an eccentric gear creates an irregular motion of the central cone. As the cone moves around, it opens and then closes the space between it and the bowl around the outside, which is often called the crusher’s “concave.” This allows rock to fall down into the wide space, then crushes it as the space shrinks. This process continues until the rock pieces are able to fall all the way through the gap between the cone and bowl and then out of the machine.
Cone rock crushers can handle a high level of throughput, but they can’t take highly variable sizes of materials – they require rock that fits the capacity of the machine. However, the cone crusher can’t produce highly uniform product, either. With a cone rock crusher, you typically need a primary crusher before them, and then a screen and/or another rock crusher afterward.
There are many advantages to cone crushers that make them popular despite their limitations. These are relatively inexpensive machines to purchase. Plus, the operating costs are also very low, and they are able to handle a very high throughput, which makes them profitable to operate even if you rely on other crushers, too.
Let Power Screening Help You Find the Right Rock Crusher for Your Operation
If you are looking for a rock crusher across the Rocky Mountain region, Power Screening is here to help. We have locations in Colorado, New Mexico, and Utah, which also serve people in Wyoming, Nebraska, Kansas, and even southern Idaho.
Power Screening has been supplying heavy equipment since 1984, and our staff includes many knowledgeable experts who can help you figure out the best equipment for your operation. This includes making the hard decision about whether it makes more sense to rent or buy your equipment. We even have quality used equipment as a more affordable option if your operation doesn’t have the capital to purchase new equipment.
Call us or use our online form to request a quote today.