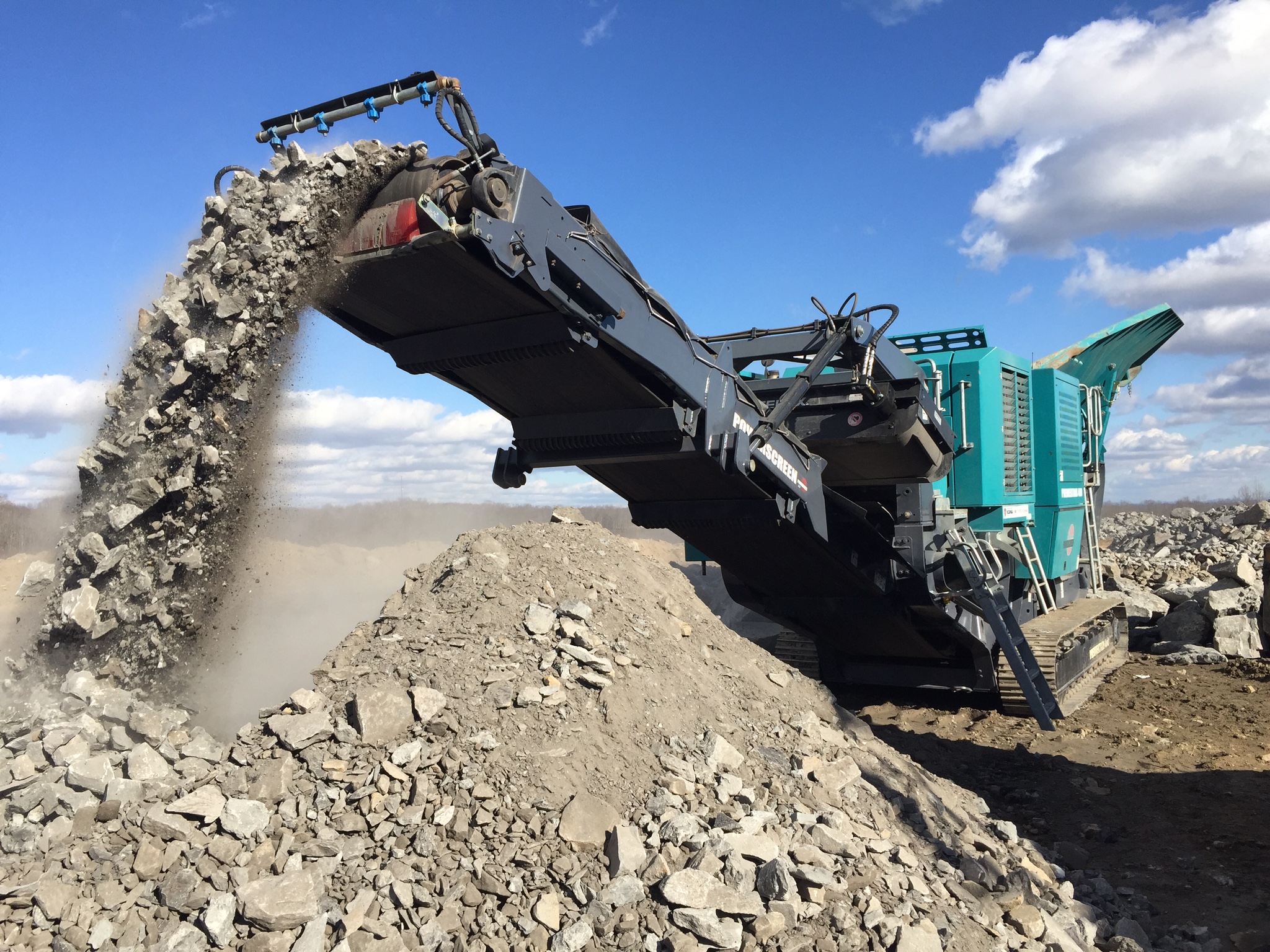
There are several different rock crusher options, and each is used for slightly different purposes. When choosing a rock crusher for your operations, it’s important to first identify the stage of crushing you’re using the machine for. This will determine the appropriate solution for your needs.
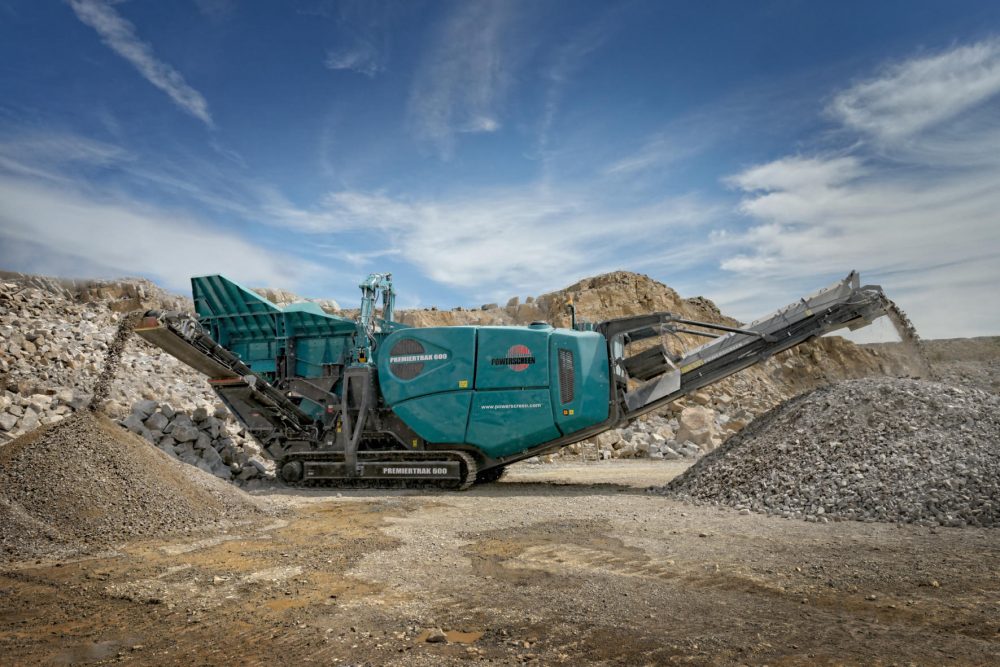
Impact, Cone, and Jaw Crushers from Power Screening Equipment
Rock Crushing Stages
There are three different stages of concrete crushing:
- Primary – This stage involves crushing coarse materials in order to allow them to be transported on a conveyer belt. These machines need to be able to handle a large capacity and accept the raw materials without suffering a blockage.
- Secondary – In this stage, the coarse materials produced during primary crushing are broken down even more in preparation for final crushing. The purpose of secondary crushing is to achieve the greatest possible reduction in particle size for the lowest possible cost.
- Tertiary – This stage further refines particles to make them as fine as possible. The quality and quantity of fine products must be considered when determining the right concrete crusher for this phase of the process.
Additional Criteria for Choosing a Rock Crusher
In addition to identifying the proper stage being used with your rock crusher, you should consider the following criteria:
- Abrasiveness and hardness – What type of material are you trying to crush? You must know the abrasiveness and hardness of the material in order to determine the maximum force or compressive strength the material can withstand before it breaks.
- Dimensions – You need to identify the maximum length, width and thickness of the materials entering your rock crusher.
- Granulometric requirement – What grain size are you trying to achieve after crushing is complete?
- Capacity – You’ll need to determine the processing capacity required for your needs.
Rock Crusher Options
Once you’ve evaluated the criteria discussed above, it’s time to choose a rock crusher that will effectively address your specific applications. Each of the following options will deliver different results and are ideally suited to different stages of the process.
Jaw Crusher
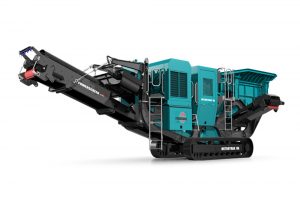
Power Screening Equipment – Jaw Crusher
A jaw crusher is a type of compression crusher that is most commonly used for primary crushing. The material being crushed is squeezed between a stationary piece of steel and a moving piece of steel. This produces the coarsest material since the rock is being crushed along its natural lines of weakness. Jaw crushers are effective the hard and abrasive materials such as granite, ores and recycled concrete.
Advantages of jaw crushers include:
- Reduces raw materials to a size of 150 mm
- Maintenance and operating costs are relatively low
Drawbacks to this option include:
-
- Not able to produce grain sizes smaller than 150 mm
- Cannot handle materials that have clay or metal mixed with rock
Cone Crushers
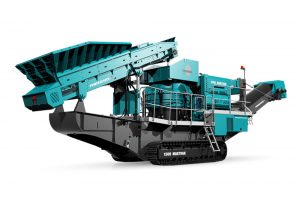
Power Screening Equipment – Cone Crusher
As with jaw crushers, these machines are compression crushers that use a stationary and moving piece of steel to break up the material. Cone crushers use a rotating head to crush the rock within a steel bowl. After initially being broken down in this manner, the material will travel through a narrow opening at the bottom of the bowl to achieve a finer grain size.
Cone crushers can be used with a variety of materials, ranging from medium to hard. They are typically used with secondary crushing, especially when the final shape of the crushed material is important.
Advantages of cone crushers include:
- Easy to adjust
- High productivity output
- Sturdy construction
- Affordable
- Low operating costs
Drawbacks to this option include:
- Inability to accommodate materials of all sizes (materials must be 200 mm or smaller before entering the concrete crusher)
- Inability to produce a homogeneous finished product
- Cannot handle clay or metal mixed with rock
Impact Crushers
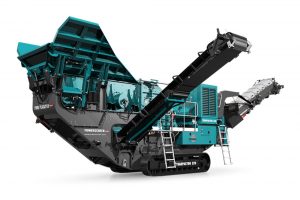
Power Screening Equipment – Impact Crusher
Impact crushers break down material by leveraging mass and velocity. The material being crushed is hit by hammers. This material then travels towards a metal plate, where the rock breaks apart and bounces back up to be hit by the hammers again. This process continues until you’ve achieved your desired final size.
Impact crushers can be used with all three stages of crushing. While they can handle materials of all hardness, they are ideally suited for soft to medium rocks.
Advantages of impact crushers include:
- Greater ability to control the final size of the crushed materials
- Can accommodate clay, dirt or metal mixed with the rock
- Produce a more uniform grain size
- High production capacity
Drawbacks to this option include:
- Higher operating costs
Stationary vs Mobile Jaw Crushers
When purchasing a jaw crusher, you can choose between a stationary option and a portable jaw crusher. Stationary crushers are typically sturdier. However, you’re limited by the fact that it must reside in one place all the time. Mobile jaw crushers, on the other hand, give you the ability to move the machine to the precise location where you need it at all times. For this reason, they often provide a more versatile solution.
Power Screening Can Help
At Power Screening, we have over 35 years of experience providing exceptional quality rock crushers to businesses throughout the Rocky Mountain region. We make customer service a top priority, and this includes making sure you have the right equipment for your specific application. As your dedicated partner, our team will take the time to understand your unique needs in order to ensure you purchase the right equipment to deliver your desired results.
Contact us today to learn about your rock crusher options.