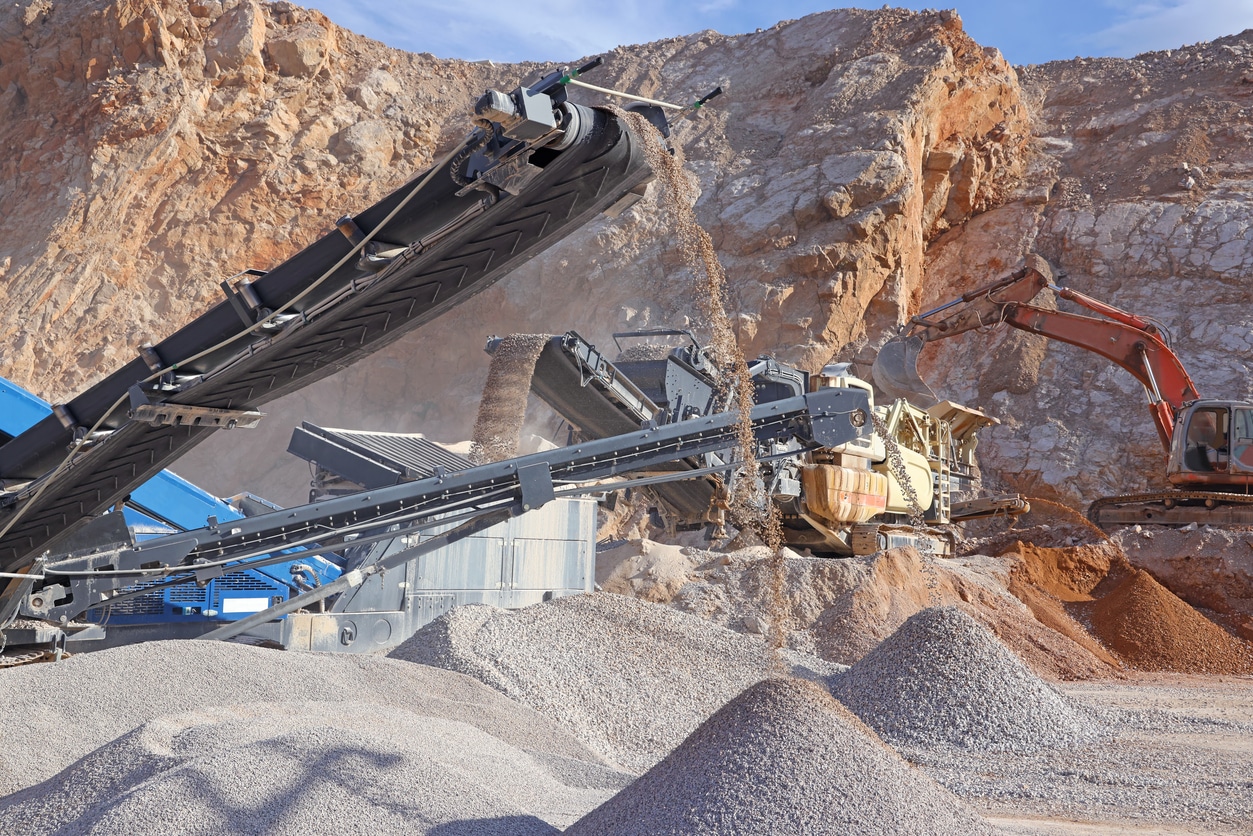
Rock crushing and screening equipment is a natural pairing. Although crushing equipment can produce smaller rock, it doesn’t always produce uniformly sized pieces. Screening equipment sorts the pieces to deliver the desired size pieces for your applications.
Here’s a brief guide to the different types of crushing and screening equipment so you can find the right pairing to make your operation efficient and effective for any type of job.
Rock Crushing Equipment
Rock crushing equipment is designed to be durable and process large rocks into smaller rocks. Rock crushers come in different styles
Impact Crushers
Impact crushers have a spinning impactor that hits rocks, breaking them into pieces. Pieces that are small enough can leave the crusher, but larger pieces stay inside the crusher, bouncing around until they are small enough.
Impact crushers can achieve high levels of reduction in size. This makes them a suitable primary crusher, taking material directly from the quarry. However, they are limited in the final size of product they produce, which means they are only suitable as a finishing crusher for relatively large aggregates.
However, impact crushers don’t produce very uniform product, and their production volume is relatively low. They are also relatively expensive to operate.
Jaw Crushers
Jaw crushers work like a jaw, opening and closing to crush rocks. The crushed rocks move from the large opening at the top to the smaller opening at the bottom.
Jaw crushers can handle relatively large rocks at the input, which makes them great primary crushers. However, their product is not especially uniform, either in size or shape, so they are not good finishing crushers.
Jaw crushers are initially inexpensive, but their operating cost is relatively high.
Cone Crushers
Cone crushers have an outer bowl, called the concave, and an inner cone, called the mantle. An elliptical gear causes the mantle to move back and forth within the concave, creating spaces that grow and shrink, crushing rocks and allowing them to fall down to narrower areas where they get crushed even smaller. When the rocks are small enough, they can escape the opening in the bottom.
Cone crushers require relatively small inputs. They are also sensitive to contaminants, which can damage the concave or mantle. This means that they are not good primary crushers, and require that their inputs be pre-crushed, pre-screened, or both.
However, cone crushers have a high production rate. They can process twice the tons per hour of other crusher types, and they produce more uniform products. This makes them great finishing crushers.
Cone crushers are relatively expensive to buy, but less expensive to operate because they are durable – as long as you protect them from damaging inputs.
Rock Screening Equipment
Screening equipment separates rocks by size. They separate large rocks from smaller ones. However, there are several different ways these rock screens operate.
Static Screens
Static screens are simple screening plants, which use either a mesh or grizzly bars to separate the larger items from the smaller ones. Large items get stopped and small items fall through.
The screens can be horizontal to collect the large items or inclined to allow large items to slide or roll off to the side.
Scalping Screens
Scalping screens typically use grizzly bars to separate large and small items. The bars are typically inclined to encourage large items to travel down to a conveyor at the end. The bars also shake vigorously to encourage more items to fall through.
Scalping screens work quickly and give a good rough sort of items. The largest items are reliably sorted out, but smaller items that fall through are not uniform in size or shape. Scalping screens are a good way to pre-sort items before they enter a rock crusher or go to a precision screening plant.
Precision Screens
Precision screens use a mesh or perforated metal conveyor to sort large items from small. These conveyors move more slowly than scalping screens and use less vigorous shaking. This helps ensure that the items passing through the conveyor are most likely the desired size in all three dimensions. This makes the products highly uniform in shape and size.
Precision screens can be set up to produce multiple sizes of output. These final products are typically ready for sale or use as they are. Many precision screen plants can even wash the sorted rocks, so they are sale ready as they come out of the plant.
Get the Right Rock Crushing and Screening Equipment
If you are looking for rock crushing and screening equipment, an expert can help you find the one that’s best for your operation. Since 1984, Power Screening has been helping people get rock crushing and screening equipment. We deliver heavy equipment in Colorado, New Mexico, and Utah. We’re not just familiar with the equipment we deliver, but also with the rocks in the area. Let us know where you’re operating, and we can match the equipment we recommend to the types of rocks you’re likely dealing with.
We don’t just deliver equipment that’s high in initial quality, either. We are in this for the long haul – we couldn’t have lasted 40 years if we weren’t – and that means helping our customers get decades of use out of their equipment. We can help you with the maintenance you need to keep your equipment operating properly for as long as possible.
Not ready to take the plunge by investing in a new rock crusher or screener? We also have rock crushers for rent and sell used equipment.
Want to find the right rock crushing and screening equipment for your operation? Please contact Power Screening today to talk to our experts.