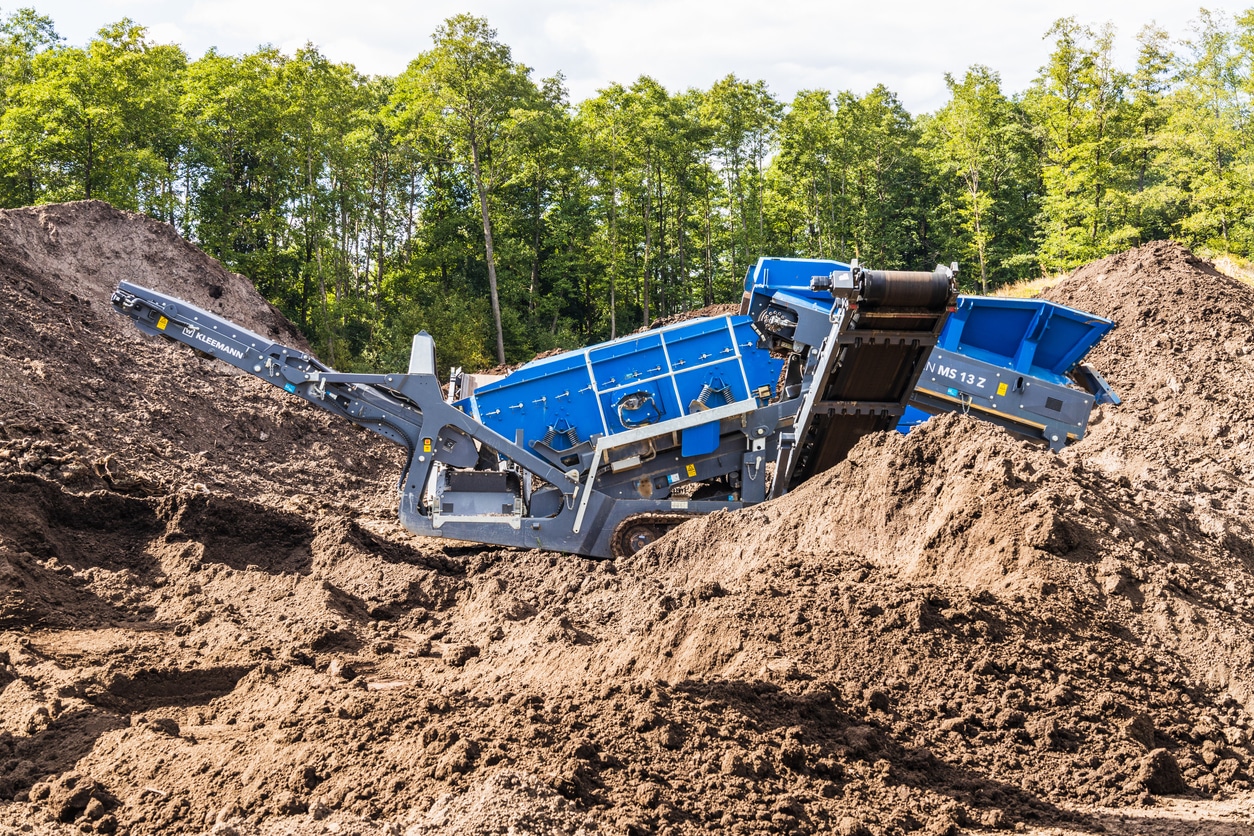
Screening equipment is one of the most essential tools in the aggregate industry. However, if you don’t have a lot of experience with aggregates, you might not know why screening equipment matters. Screening equipment is also used in related industries for similar functions, so understanding how it works in the aggregate industry can give good insight into the general function of screening equipment.
Screening equipment is used to separate materials by size. It’s like using a sifter at home to separate out the large particles in your processed flour.
Why Size Matters for Aggregates
Aggregates are used in numerous construction applications. This includes mixing with cement to make concrete or with asphalt for road and other surfaces. Aggregates provide additional strength in these applications. In other applications, aggregates might be used on their own as a fill material to promote drainage or even to provide filtration. In all of these applications, the size of the aggregate matters.
Aggregates come in a wide range of sizes and size distributions, but each one is designed for a specific reason.
In applications where aggregates are added to provide strength to concrete or asphalt, the goal is typically to have a distribution of sizes that minimizes the creation of voids and spaces that can weaken the construction. In applications where aggregates are added for drainage, on the other hand, the goal is to create voids, so the tendency is to try to make the particles of a uniform size and shape to create voids that allow water to flow through. In all applications, there is a desired maximum and minimum size of particle, so processing typically includes washing, which is itself a type of screening to remove very small particles.
Aggregates Start with Unpredictable Sizes
The challenge in the aggregate industry is that natural sources quarried for aggregates typically produce an unpredictable distribution of sizes.
Digging in your yard, you likely come across all manner of stones, twigs, broken pieces of concrete, maybe even an old toy or bottle. Someone buying topsoil would be very unhappy to find they’ve paid for a volume of topsoil that contained a significant amount of these contaminants.
Likewise, if you’ve ever taken the time to find skipping stones at the edge of a river or lake, you’ve probably noticed how widely distributed the size of rocks can be. Sometimes they sort into a relatively uniform distribution, but often they aren’t. Delivering rocks of the size distribution found by a river might be reasonable for aesthetic purposes, but in construction applications, there is no guarantee that you would have a distribution of sizes that promoted strong concrete or allows proper drainage.
Often, construction applications use crushed rock. The rough broken rock faces provide greater surface area and friction to help strengthen concrete and other materials. Rock crushers are used to create these materials, and they can be set to create rock of a certain size. However, rock crushers typically create a wide distribution of rock sizes, with many smaller rocks produced along with those at the maximum size set by the crusher operator. There’s no guarantee that the rocks emerging from the crusher will have the desired size distribution.
In all of these cases, providing the desired product requires sorting the harvested material, which is what screening equipment is for. Sorted fractions might be discarded if undesirable or remixed to provide the desired mix of sizes.
How Screening Equipment Works
Screening equipment uses relatively simple principles to sort materials. Essentially, the screen has holes in it, and material that is too large to go through the holes gets separated from what is small enough to pass through.
However, there are a few common ways that screening equipment performs the separation.
Static Screens
With static screens, the material to be separated is poured onto the screen, and it either falls through or doesn’t. This screening process is relatively inefficient and is often used only for rough sorting.
Linear Motion Screens
Linear motion screens typically use a combination of vibration and forward motion to encourage material to fall through the screen if it is small enough to fit through in at least one dimension.
Screening equipment often includes multiple screening stages to separate products into different size categories, effectively producing two, three, or four aggregate products simultaneously.
Rotating Screens
Some screening equipment uses a rotating drum to separate materials. Known as trommel screen or drum screen, the drum motion constantly agitates the material to encourage the passage of small pieces, while keeping large pieces inside the drum.
Whether a linear or rotating screen is best depends on your application.
Get Screening Equipment in the Rocky Mountain Region
If you are looking for screening equipment or other aggregate equipment, let Power Screening help.
Since 1984, Power Screening has been helping people in the aggregate and construction industries get the equipment they need to run an efficient and profitable operation. Our knowledgeable experts can listen to your description of your operation and help you find innovative solutions that will help you be productive and efficient.
If you only need equipment for the short term, perhaps even just one job, we offer a wide selection of well-maintained rental equipment that works like new. If you are ready to invest in a long-term solution, we can help you find the reliable equipment that you can depend on for years to come. Further, if your budget is tight and you are looking for a bargain, we offer used equipment for sale that functions like new and has many useful years left with proper maintenance.
We cultivate close relationships with the manufacturers of the equipment we sell. That helps us match our customers with the exact equipment they’re looking for as well as provide factory-authorized quality service when necessary.
To learn more about how Power Screening can help fulfill your equipment needs, please contact us today.